![]() |
Inventory is an essential component for the smart functioning of any business. An organized inventory management model can pave way for the increased lifetime value of your customers by ensuring timely delivery of products without any disruptions. Apptivo has a definite supply chain system that helps companies with their inventory management. While integrating with Apptivo will simplify your process, there are certain general practices which when applied will further enhance your inventory management.
Inventory management is not a simplified task. Rather, it is an integrated system bringing together a complete workflow right from placing purchase orders, obtaining items, approving orders, generating invoices, to dispatching them to customers. According to Research, about 34% of businesses cited that accepting orders for products not in stock is a reason for delayed delivery. This might force customers to quit purchasing products from you the next time. Also, this sheds light on the importance of inventory management. Had these businesses kept a close watch on their inventory, they could have easily refilled the stocks, accepted the orders, and avoided delayed deliveries.
In this blog, we will break down some techniques for spotless inventory management in your business.
What Is Inventory Management?
Inventory Management (Stock Management) is the process of levying a systematic method to manage your inventory. It includes the sourcing, storing, and selling of your products and updating your inventory in real-time. In simple terms, it is making sure that the right products are available for sale at the right time.
Picture this: David plans to open a new diner at the center of his town. After locating a place and getting everything set, he goes to suppliers to purchase the products required for preparing the items on his menu. This can be flour, meat, or any ingredient that is part of the menu. When he buys the products, they become part of his inventory. Once customers start coming in, he has to keep a keen eye on the inventory. This will ensure that no ingredient is missing and customers are not left disappointed. For this, using the pen and paper method is challenging as the data are not updating in real-time and this can cause double entry or mismanagement. To avoid this, businesses can sign up for inventory management software for a smooth workflow.
Inventory Management – Key Techniques
Implementing a detailed process management system for your inventory is worth the investment. When you utilize an Inventory Management App, you will notice better productivity and management. Hence, we have listed few techniques that you should keep in check for efficient stock management.
Just-in-time Inventory
Just-in-time inventory is an inventory management technique that helps to increase efficiency, reduce maintenance costs, and make the items available only when they are needed. Originally invented in Japan, Just-in-time is a common inventory management method to streamline your Supply Chain workflow.
It is basically keeping the inventory in check by negating the risks associated with maintaining a larger inventory over a period of time. In this technique, the supply system keeps the suppliers informed of the schedules and places orders only when they are actually necessary. This reduces the effects of dead stock.
ABC Analysis
In ABC Analysis, your complete inventory is divided into three categories A, B, and C according to their priority. Here, all the materials that are of high importance in your organization fall under the ‘A’ category. The items that are of lesser importance than the ‘A’ category fall under the ‘B’ value category. Lastly, ‘C’ category items are of least priority and have a less monetary value.
Based on the ABC analysis, you can identify the items that have a greater impact on the supply chain and help your teams to focus on the availability of those items and inventory costs. It will help teams to prioritize the purchase orders of items according to the inventory costs. By focusing on the ABC analysis, businesses can notice increased productivity in their inventory management.
Backordering
Backordering works along with the Just-in-time inventory technique. Backordering is placing orders for items that are not present on hand. It involves companies predicting the surge in sales accurately and being prepared for upcoming orders. While the Just-in-time technique decreases inventory maintenance costs, Backordering prevents customers from receiving delayed orders.
The situation of backorder occurs when the demand is more than supply. More the number of backorders, the higher the demand for an item. These backorders are strategically placed to suppliers to ensure quick delivery of products.
Cross-Docking
Cross-Docking is a technique where the items are directly delivered to the customers rather than moving them to multiple warehouses. This creates a situation where there is no requirement for storage and no handling time. Alternatively, this reduces the maintenance costs of items and prevents them from damages.
Imagine you are running a fresh food business, where you obtain the items from your suppliers and sell them to your customers. When you store the items in your warehouse, it might affect the longevity of your products. Hence, these companies normally load the products to another truck once they receive them from suppliers. This is a classic example of cross-docking.
Demand Forecasting
Demand forecasting is the procedure of estimating customer demand based on historical data. In this method, companies forecast the demand for their products and services in the future based on their previous sales history. In this, businesses use scientific methods to calculate the requirements based on certain indicators.
Forecasting is not an uncommon process in the supply chain system. However, a deeper understanding of the demand assists companies to devise their entire business workflow for the next month, quarter, or year. By this, businesses can determine the items, labor, types of equipment, and other factors while assessing the company’s budget.
Conclusion
When you have an efficient distribution management system, you can overcome any unforeseen losses and maintain good profits for your company. The above-listed inventory management techniques help companies to take appropriate measures while placing customer orders, purchasing items from suppliers, and delivering the right products at the right time. The detailed distribution management software of Apptivo assists your business in getting things right and increase your customer satisfaction.
Frequently Asked Questions
- How to create a Miscellaneous issue from Inventory Management?
- How do I Create Warehouses?
- How do I create Shipment from the Inventory app?
Latest Blogs
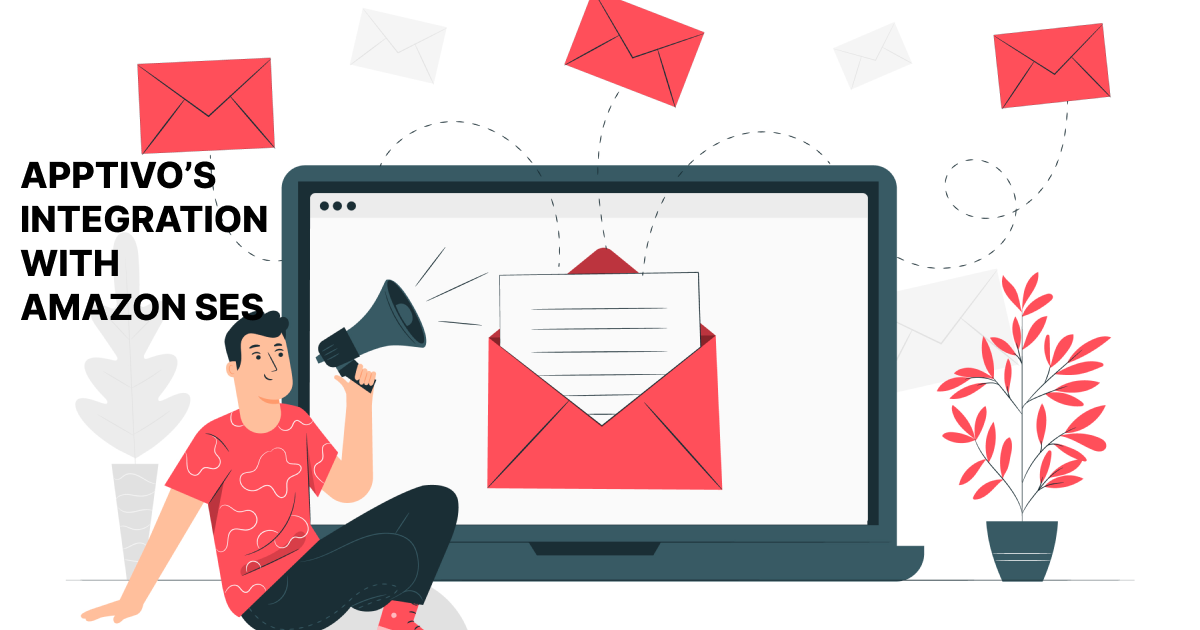
Apptivo's Integration with Amazon SES for Outgoing Email Server
Amazon Simple Email Service (SES) is an email platform that provides an easy, cost-effective way to send and receive email using your email addresses and domains. Apptivo has migrated its email service to Amazon SES (Simple Email Service) to enhance the performance and reliability of our email services
Read more →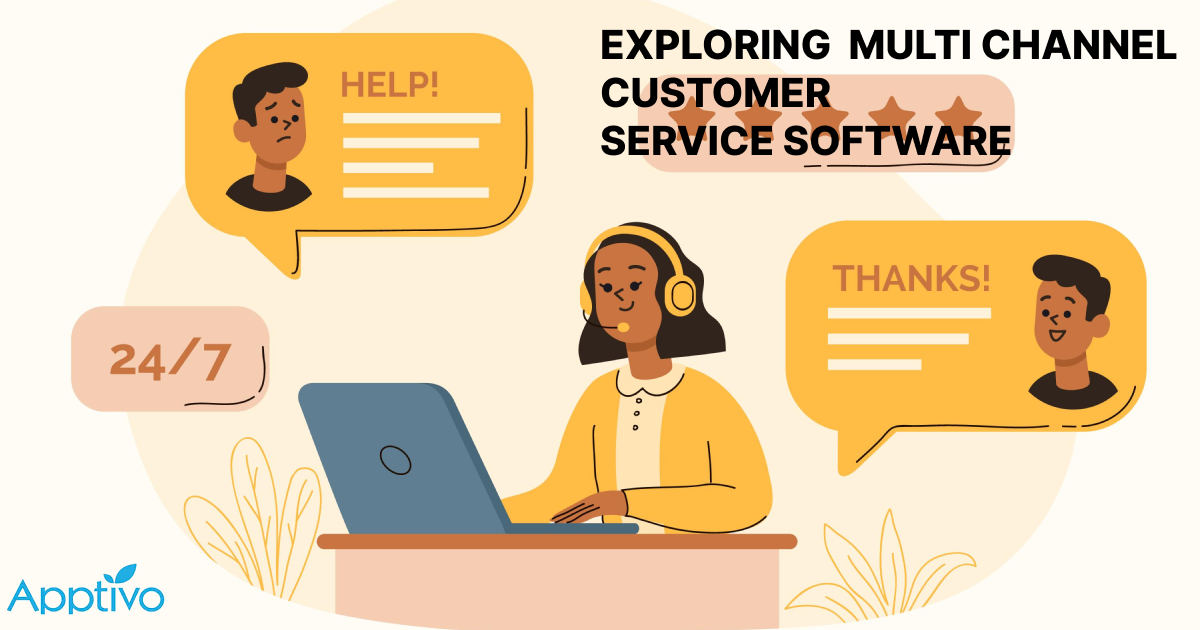
EXPLORING MULTI CHANNEL CUSTOMER SUPPORT SOFTWARE
1.What is customer service software? 2
Read more →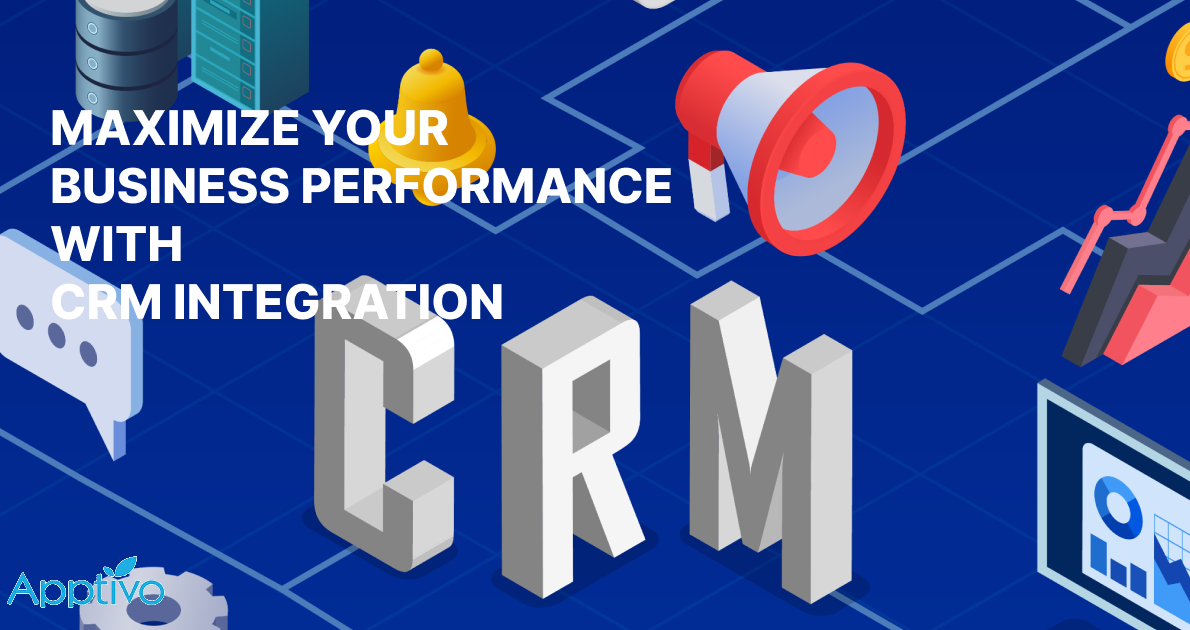
Maximize your business performance with seamless CRM Integration
1.What is CRM Integration? 2
Read more →